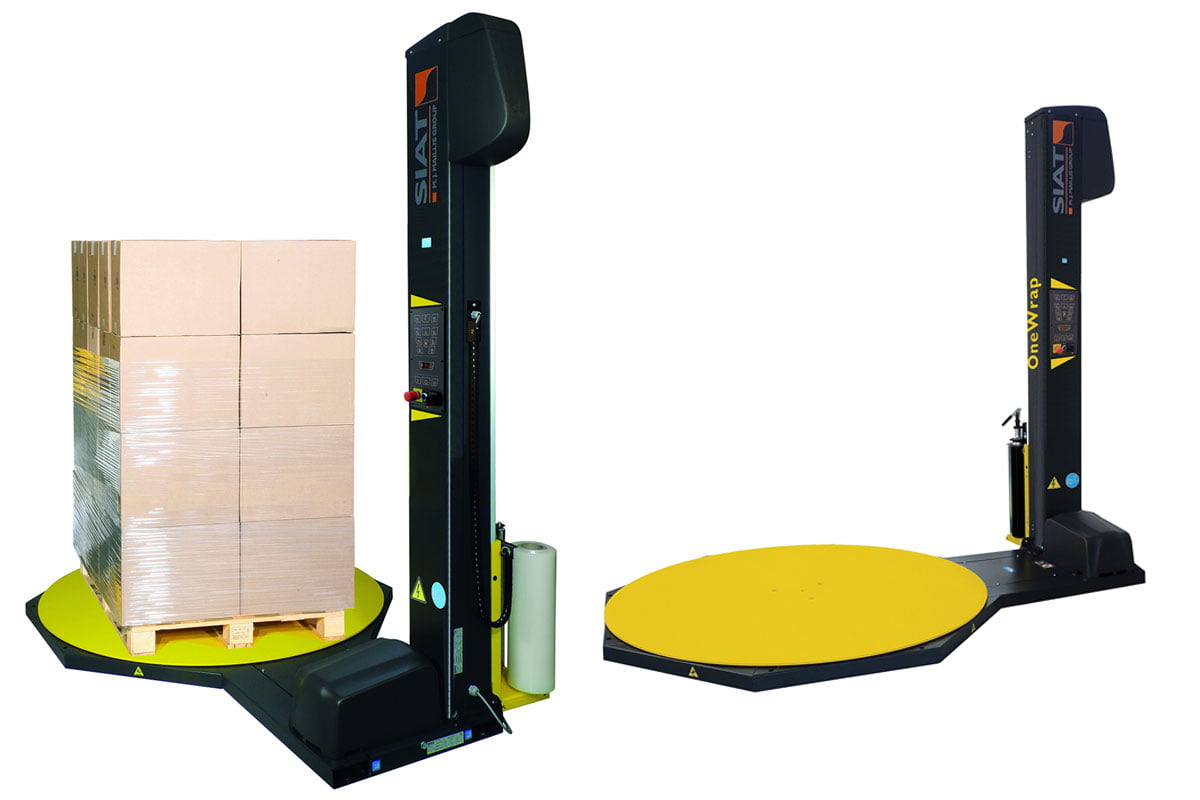
7 Mistakes People Make When Buying a Pallet Wrapper
– And How to Avoid Them
Hindsight is a wonderful thing!
As someone once said: “if I’d known then what I know now, I wouldn’t have done what I did then and I’d probably have saved myself time, money and heartache”.
Like so many things in life, we often don’t know what to expect from items that we buy until we have bought them, and then it’s usually too late to go back. This blog is an attempt to outline a number of mistakes that people make when buying a pallet wrapper and to suggest some of the questions it is sensible to ask in order to avoid making these mistakes. I am sure that there are many more mistakes which can be – and are – made when buying a pallet wrapper but the seven listed below are, in my opinion, the seven most important to get right.
- It is very important to get the right machine for the job and to get a machine that can cope with the amount of work you intend to give it. There are two main types of pallet wrapper:
- An automatic machine, situated at the end of a production line. The pallet rolls onto the wrapper, is wrapped, and then rolls off the line without human intervention. This type of machine is generally seen in large factory manufacturing environments.
- A semi-automatic machine. This is the most widely seen and sold pallet wrapper. It usually has manual and automatic wrapping cycles which can be selected by the operator.
Now it should be obvious which of these best suits your needs. This document is intended for those in the latter category; those in the former require individual specialist design and engineering advice. So let’s consider the semi-automatic machine.
There are three main types of semi-automatic pallet wrapper:
- A core brake machine. A mechanical brake prevents the roll of stretchwrap from running freely on its mount, generating tension between the pallet and the roll and so stretching the film onto the pallet.
- A machine with an electromagnetic brake. This operates in much the same way as the core brake machine but the tension is set by pressing a button on the control panel. An electromagnetic brake operates on the reel and – depending on the amount of current applied – tightens or slackens the friction applied by the brake and thus the tension applied to the film.
- A machine with a power pre-stretch unit; the most sophisticated type of semi-automatic machine. The pallet wrap runs through a set of individually-braked rollers which stretch the film before it leaves the stretch wrapper. This type of machine is generally much more expensive than either of the others and requires a more expensive film to gain the maximum benefit. However, the machine allows the film to be stretched much more than a standard film, making it much thinner before being applied and therefore using less film to reach each pallet – hence reducing cost!
It is now possible to buy pallet wrap that has been pre-stretched during its manufacture, enabling you to obtain results close to those achieved by a machine with a power pre-stretch unit from a simple core brake or electromagnetically-braked machine.
The type of semi-automatic machine that you choose will probably depend on the number of pallets that you wrap per day or week. A machine with a power pre-stretch unit is usually much more expensive than its more basic counterparts and will require higher throughputs in order to justify the extra purchase costs and the more expensive film. Having said that, for high throughputs it will generally be the most cost-effective machine.
- Pallets come in all shapes and sizes and so do pallet wrappers. Part of the process of deciding which pallet wrapper is best for you is to think about the biggest base size and the tallest pallet that you will wrap. Weight is also a consideration, but most good pallet wrappers will take pallets of up to two tonnes.
- It is possible to get pallet wrapper turntables in a number of sizes. The UK standard nowadays is a diameter of 1.65m as this will accommodate the most widely-used UK pallet with dimensions of 1.2m x 1.0m; this gives a measurement across the diagonal of 1.56m, so the pallet fits neatly on the turntable with no overhang. It is also possible to purchase machines with turntables of 1.5m diameter – suited to euro pallets – and 1.8m diameter which are necessary for large pallets used for transporting products such as animal feed.
- The height of the mast of the pallet wrapper is obviously vital when determining the maximum height to which a pallet can be wrapped. Most standard wrappers will wrap to just over 2m but it is possible to specify a taller mast if it is necessary to wrap higher.
Whilst it is possible to vary your combination of turntable diameter and mast height, it really is vital to do this when you order the pallet wrapper; to do so after delivery is not impossible but is likely to prove financially prohibitive.
- Another major consideration is whether to have the pallet wrapper recessed into the floor – so the turntable is level with the floor – or for it to be free-standing.
Recessing the machine requires excavation of the existing floor (unless you are installing into a new build, in which case think ahead and allow room!) in order to accommodate a pit frame which is bedded in concrete and into which the pallet wrapper is then inserted.
A free-standing pallet wrapper can be supplied with a ramp to allow pallets to be placed on the turntable manually with a pallet truck and in most cases has the additional benefit that, if working methods alter, the machine can be easily relocated to another part of the factory or warehouse.
- Give thought to what you are wrapping and the variation that you may require for wrapping different products. Machines come with a variety of programmes and options, such as the ability to add a top sheet prior to, or during, the wrapping cycle. Generally the more programmes and the more options you require the more expensive the machine will be, but it will usually cost more to add functions after you have taken delivery of the machine than if you specify functions prior to purchase.
It is also worth considering whether you want operatives to be able to adjust settings on the machine or to leave this to the supervisor or controller of the unit: this depends on the number of people that will operate the machine and their level of skill. Constant changes to the settings will undoubtedly result in more wrap being applied to pallets than the optimum, resulting in increased wrapping costs and so defeating one of the main objectives of purchasing the pallet wrapper.
- Be extremely careful not to be taken in by companies offering unbelievably cheap prices but insisting that you buy the pallet wrap from them. Always remember the old adage that “there is no such thing as a free lunch”: there is no such thing as a free pallet wrapper and if the machine appears ridiculously cheap it is probably because you’re paying over the odds for your pallet wrap as part of the deal.
It’s always a good idea to see if the company you are considering buying from will let you have the machine on trial for a week before you buy; they should also be prepared to try several types of film on the machine and to tell you how much it will cost you to wrap each pallet, so you can find the stretch wrap that suits your products and your budget.
- Another serious consideration, often overlooked, is servicing and breakdown cover. Check that the machine you are considering comes with at least 12 months’ parts and labour warranty. Depending on how many pallets you are wrapping each week, consider how often you should have the machine serviced and – if you are producing a product which must be sent out every day – you may require breakdown cover. Can your intended supplier assure you that in the event of breakdown they have engineers who will come out to repair the machine and that they carry spare parts to fix most eventualities? It is often worth speaking to people who have bought a wrapper from your prospective supplier 12 months or two years previously and asking what their experience of the company’s service has been.
- Finally, when you’re happy that all the questions have been answered to your satisfaction, the most important question is how you are going to pay for it; indeed what is the best way to pay for it. The answer is that there is no definitive right or wrong way to pay for the machine; it depends very much on your circumstances.
The three alternatives to consider are:
- Outright purchase
- Lease purchase
- Lease rental
Each of these payment methods has different tax and VAT implications. You need a supplier or a bank that can provide you with the alternatives. In most cases your accountant should be able to suggest the right course of action for your business’s particular requirements.
I hope that these pointers will prevent you from falling into the pitfalls waiting for the unwary. If you would like to speak to someone in person we are always willing to discuss your requirements at Agritel. Just call 01691 671496.