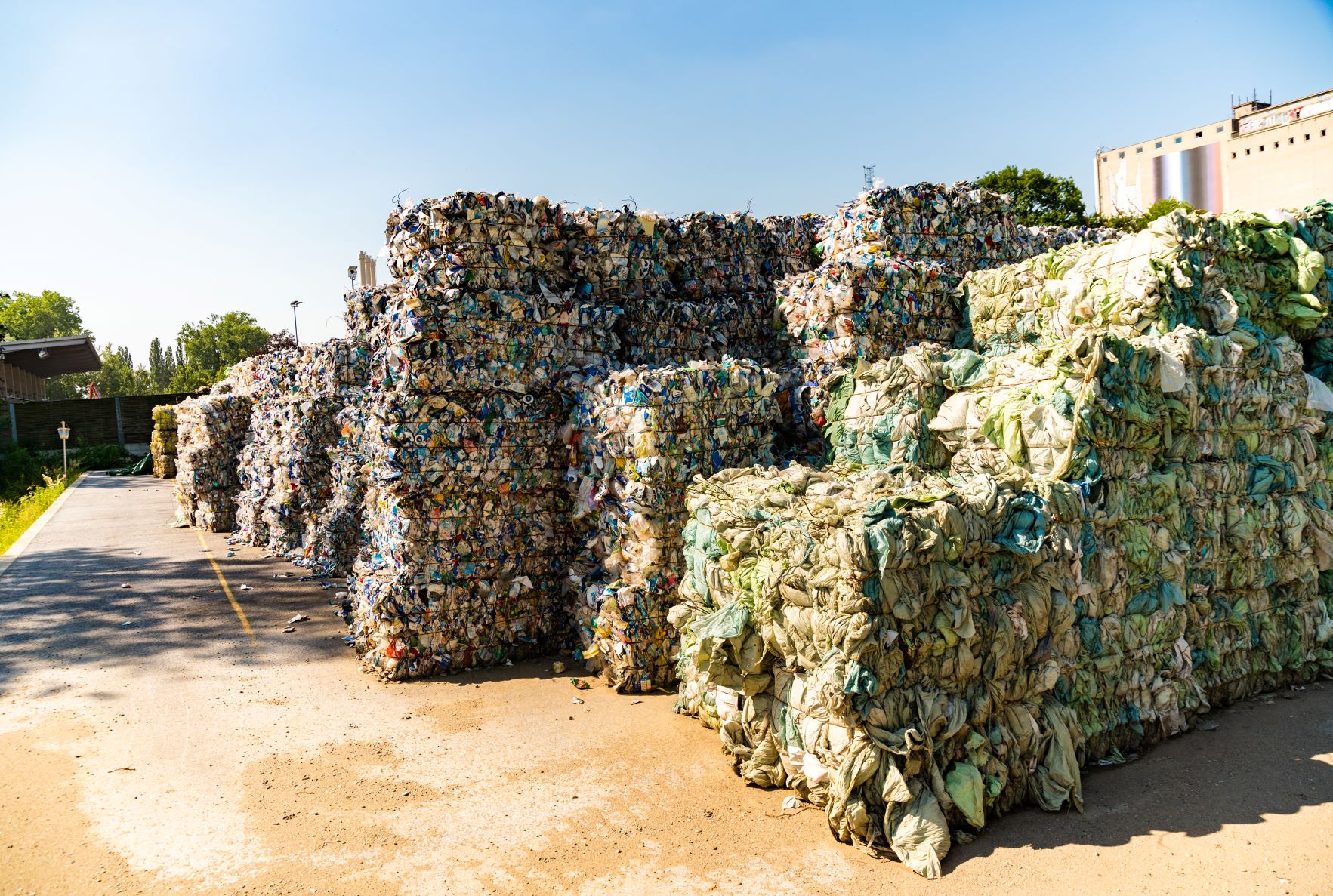
When deciding on the next piece of equipment for your business, a waste baler or crusher probably isn’t the first item on your list. However, if your business often deals with carboard, plastic and metal can waste, you’ll notice that your bins can fill up very fast and require frequent collections. Not only are you paying for the disposal of air inside the uncrushed waste, but you’re potentially also sending recyclable material to the landfill. Cardboard, metal, and many plastics can be recycled and reused. Therefore, an automatic waste crusher or baler can not only save your business money by reducing waste transport, but it can also help the environment. This article looks at the benefits of a waste baler or crusher:
The Benefits of a Waste Crusher or Baler
- Reduces the amount of bin space used by removing air
- Reduces the number of waste collections
- Reduces a businesses/organisations impact on the environment
- Helps to keep the workspace clean and tidy
- Helps prevent recyclable material being sent to landfill
- Extremely easy to clean and require minimal maintenance.
Here is a video of the Ag-mac V60 Waste Baler in action. The V60 is one of our most popular balers. It’s ideal for locations where space it at a premium: garage forecourts, retail outlets, offices, shops, pubs, restaurants, and light industrial applications for example.
Businesses and Organisations Benefiting from a Heavy-Duty Crusher or Baler
- Restaurants and pubs
- Shops and supermarkets
- Car garages
- Hospitals
- Manufacturers
- Builders
- Schools
- Festivals.
Business Case Studies
Case Study 1: A smashing time at Jamie’s Italian
Noise from bottles being emptied into wheelie bins late at night can be a major problem for your neighbours if you have a busy city centre restaurant. The space taken up by bottles can also be a major problem for you if your restaurant is in the heart of the city of London and space is at a premium.
Jamie Oliver’s new restaurant at 17 Denman Street, Piccadilly is such a site. They have solved both problems though at one fell swoop by installing a bottle crusher from Agritel. The glass bottle crusher, housed in the basement of the restaurant, smashes bottles to a fifth of their volume before discharging the broken glass into a wheelie bin which can be easily moved to a collection vehicle when full.
Case Study 2: Bargain Booze makes space, saving time and money
Siop Bwyd Corwen Cyf, a Bargain Booze outlet in Corwen, North Wales, has derived huge benefits from installing an Ag-mac V60 Waste Baler.
Cardboard waste was becoming a problem. Bargain Booze runs a collection service, picking up waste packaging when it delivers stock to its stores. As the shop became busier, they found that cardboard awaiting collection – stacked loose or in metal cages – was occupying a large portion of one of their stock rooms. Increasing sales and limited space prompted the business to search on Google for a waste baler and, finding that Stan’s Superstore branches at St Martins and Llangollen had both purchased Ag-mac Balers, led to them contacting Agritel.
Having installed the V60, the business now crushes waste packaging as it is generated, producing compact, manageable bales. Bargain Booze collects two or three bales of cardboard every week when delivering stock, and their drivers find it easier and quicker to pick up the baled waste which naturally takes up much less space than loose cardboard.
Apart from freeing-up space and saving time, the team has found added benefits, as explained: “The baler allows us to tidy up as we go along; it removes a fire hazard posed by loose cardboard and that enables us to fulfil the necessary health and safety requirements. The machine is now part of the family!”
“Buying a baler is certainly a cost consideration for any business, but we would never go back to being without one,” adds the manager. “It isn’t easy to quantify the precise cost savings, but we believe the labour and space saving alone will ensure that the machine pays for itself. There is no costly maintenance associated with the machine and it’s safe enough that anyone can use it. Every retailer should have one!”
Case Study 3: Oil retrieval pays dividends for Biffa
A can crusher supplied by Agritel has brought improvements to waste handling at Gatwick Airport.
All of the airport’s waste is processed by Biffa Integrated Resource Management Ltd at its Gatwick transfer station site. Open all day every day, the site is small but, by necessity, extremely well-organised to prevent the build-up of the many waste streams. Anything that reduces the space needed for storage and saves money is of interest to the team. Amongst the items passing through the station are many thousands of used 1-litre oil tins, which are placed in storage safes prior to disposal. Keen to save space, the business reasoned that if the cans were crushed, they could occupy as little as one tenth of their original volume; as a bonus, any residual oil could be collected during the crushing process for recycling.
A Google search revealed Agritel’s range of can and filter crusher and, after discussion, Biffa Integrated Resource Management Ltd brought a boot-load of cans to the company’s warehouse for a crush trial. As a result, they opted for a MG15 TFL Oil Filter and Can Crusher: designed for oil filters and large, single cans, it is capable of crushing 24 1-litre cans at a time.
After the machine was installed, it was found that the circular press plate allowed the occasional can to become trapped between the plate and the walls of the chamber, so Agritel arranged for a snug-fit square plate to be supplied to solve the problem. “The machine now works well and has reduced the number of waste safes required from fourteen to only three. This has not only created space, but the waste oil recovery has generated extraordinary financial benefit, into the thousands of pounds!”
More labour is required to operate the system, but this is outweighed by income from the sale of recovered oil. The new regime has met with a positive response from the Environment Agency which has been involved from the early stages of the project, advising on all aspects of handling waste oil including the use of a bunded storage tank and operator platforms for safe transfer.
Case Study 4: Commercial vehicle repairer reduces waste disposal costs by 80%
A Leicestershire commercial vehicle service and repair business has seen an 80% cost reduction in the disposal of used oil filters thanks to the product that we supplied.
Established in 1990 and covering the Leicester and East Midlands area, Hinckley-based Truck Services (90) previously disposed of the old oil filters using a monthly skip collection, where none of them were recycled; then – subsequent to new waste disposal legislation – via a recycling company.
Seeking a way to reduce the storage space required between collections, Truck Services (90) online search found the Ag-mac OFC10 oil filter crushing machine provided by Agritel Ltd, the Oswestry company which also supplies industrial packaging materials to businesses throughout the UK.
The owner of Truck Services (90) believes the OFC10 will pay for itself within two years. He said: “We can now fit 400 crushed oil filters in a storage bin, whereas previously it would only take 65 uncrushed. Consequently, the recycling company now only charges us £38 per month for a two-bin load, as opposed to twelve bins or one skip at £235. As well as the cost savings, there are other benefits. There is more space in the workshop and it’s tidier, and the oil recovered from the filters using the OFC10 can also be recycled, which adds to our good feeling of doing something for the planet!”
Case Study 5: Ag-mac Drum Crusher creates space at Kerax
Kerax Ltd, the UK’s leading manufacturer, blender and supplier of wax products, faced a space shortage at its Redditch ‘Kerax Hyperdrive’ lubricants manufacturing site. Mounting numbers of empty 205-litre drums were accumulating in the yard: even when palletised and stacked, 400 drums occupied more than 400 square feet of valuable space.
The Managing Director at Kerax felt that the answer was to crush the drums so that they could be stacked more efficiently while awaiting disposal. He looked at prices for long-term rental of a drum crusher but, as he explains: “they seemed very expensive, so I searched Google and found Agritel. When I phoned, they seemed to know what they were talking about; they quoted me a price to buy a drum crusher and told me that if I wasn’t totally happy with the machine they’d take it back and refund my money!”
“I’m pleased to say that the machine does exactly what they said it would.”
Kerax took delivery of the Ag-mac DC10 Drum Crusher which made a huge difference.
“Installing Agritel’s Drum Crusher has allowed us to clear the backlog and we can now store the same number of barrels in only 75 square feet!”
The Ag-mac DC10 crushes 205-litre (45 gallon) drums down to approximately one-sixth of their original height. Drums are compressed neatly within their original footprint, so that they can be easily – and safely – stacked or palletised ready for disposal.
Case Study 6: An Ag-mac V450 Waste Baler is saving us over £1,000 a month!
Welch Mill Carpets is a family-owned business established for over 50 years. The business employs 14 people and sells carpets, laminates, vinyl, and wood floors from a 30,000 sqft warehouse in Leigh, Lancashire. Welch Mill Carpets supply flooring to all corners of the UK, direct to both commercial and domestic end users, with the vast majority of their sales coming from recommendation by satisfied customers.
Originally, the business was spending over £2,000 per month emptying containers full of loose carpet waste trimmings, leftovers from the fitting process. “The way the waste was being handled was time and labour intensive and very inefficient,” says the owner of the business. “When I saw a baler at a Yorkshire trade show I thought: ‘this might be the solution!’”
“We searched the internet for a machine and found Agritel. Their V450 was at least £2,000 cheaper than similar models so we contacted them and bought one. We now bale all our carpet trimmings and produce around 6 bales a month. They are easy to move and store before collection by our recycler. It still costs us to have the bales removed but it’s less than half the amount it used to be, so I suppose the baler paid for itself within six months.“
Case Study 7: CV Rollers Case Study
CV Rollers, a manufacturer of high-quality roller assemblies based in Oswestry Shropshire, have made large savings after installing an Ag-Mag V75 Multi-Chamber baler bought from Agritel.
CV Rollers manufacture high quality assemblies primarily using plastic bearings, injection moulding and CNC machining, as such, they produce a large waste stream comprised of both plastic and cardboard. Having looked at their current method of disposal of placing the loose cardboard and plastic into skips and large bags, it was clear that savings could be made from installing a baler. The multi-chamber allows for loading of one chamber whilst baling in the other: perfect for sites with large amounts of cardboard and plastic waste.
The machine creates neat, space saving bales that are easy to move with a lifting trolley included with purchase. By using the baler to compact their waste, they were able to maximise the space utilisation in their skip meaning less frequent collections. “We estimate our collection costs have been reduced by 40% since installing the baler and have calculated a payback period on the machine of 14 months” said the Managing Director of the company. It has also enabled better use of their labour, as before waste would have to be loaded onto their own vehicle and taken to the local recycling company. “We used to have two employees who would load up our vehicle with loose, waste cardboard and plastic, which was extremely time consuming, we think the baler has saved four hours of employee time wasted on taking waste to the recyclers”.
Conclusion
The case studies above are a great example of how, through consultation, the perfect solution can be found to streamline a business’ waste management system and show real cost savings. While the initial cost of buying a waste crusher or baler may seem expensive, its long-term benefits are immeasurable and will ensure a more cost-efficient, cleaner and safer workplace for all involved.
Wondering what to do with your waste? Give us a call on 01691 671496 and speak to our team of knowledgeable and friendly staff who would be glad to advise you on a waste-management system perfect for your needs.